Which side of the coin is your Quality organisation ?
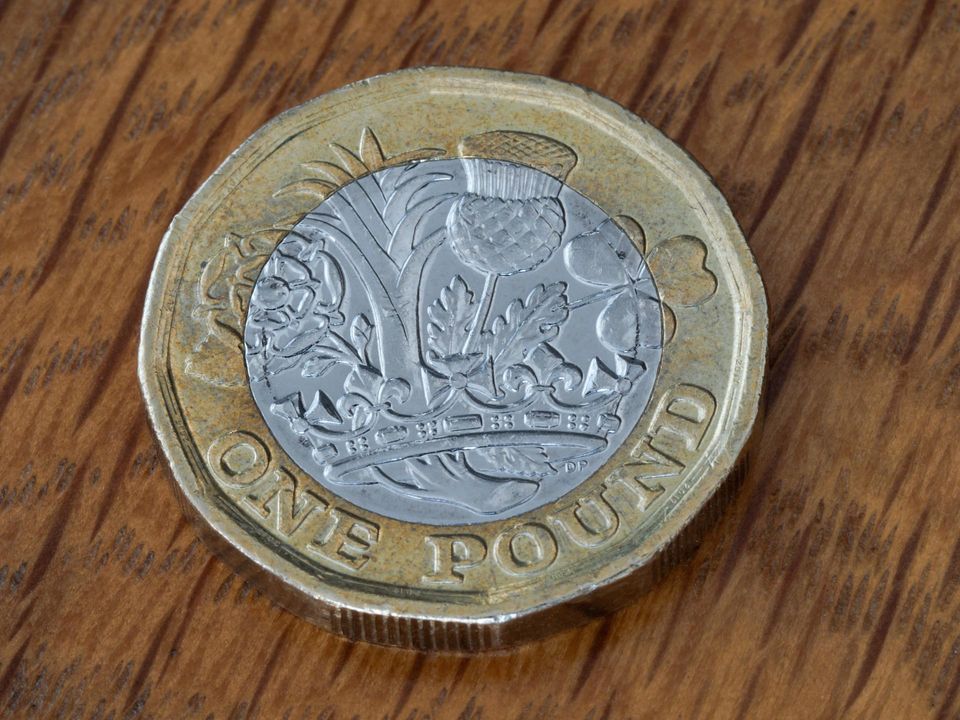
I stumbled into the world of Quality
partly by accident around 20 years ago. In truth I’m a biochemist, but don’t tell anyone.
“ Would you like a job in our Quality Engineering Group
?” a senior manager asked me. The rest is, as they say, history.
Over the years I’ve struggled to explain what my job actually entails, mainly to my family. To many a job in Quality
involves walking around with a clip-board counting things and tutting a lot. But what do I actually do ?
I make the world better. Or at least I try to.
The job I do and the business I set up - Datod
- attempts to make a difference: a difference to patients, customers, businesses and people.
Quality
as a recognised profession started in the mid 1950s, pioneered by holistic thinkers such as and Deming
and Juran. Their forward thinking approach soon became encapsulated in what became known as Total Quality
Management.
Then something bad happened. Very bad.
It is still around us, even today.
The world of Compliance was born.
I’ve nothing against compliance, so hear me out.
Suddenly Quality
diverged from what Deming
and Juran
would have recognised. Its sibling Compliance
was created.
Compliance
involves ensuring obedience to regulations and standards, making sure documentation is complete, preparing and managing for audits. In the world of Compliance
success is measured by surviving an inspection with limited observations, or whether processes within the Quality Management System are followed and delivered on time. Compliance is checking, reacting, telling
and
instructing.
Quality
involves understanding customer needs, improving, simplifying, building. Success is measured in customer satisfaction, repeat orders, jobs made easier, and lives improved or saved. Quality is about teaching, mentoring, changing
and
improving.
A survey of the use of quality improvement approaches, such as lean and Six Sigma, within the medical device industry has shown it to be historically low, with rates of around 30% and 20% respectively [1]. Which begs the question: have we taken our eye off the ball here ?
When I look at some Quality
groups today, I don’t always see Quality, but Compliance.
Compliant organisations can make some terrible, and even dangerous products. Conversely organisations that are nimble, innovative disruptors can quickly get into regulatory difficulty.
When you look at your Quality
organisation, what do you see ? How many of those working in your Quality
department know who your customers are ? Have they ever talked to them ? Do they know your customer’s biggest complaints about the services and products you are providing ?
In the real world we need both competencies, each with different and unique strengths. They are different sides of the same coin. Compliance
is showing we are doing what we must do. Quality
is doing what we should do.
Build your Quality and Compliance groups with individuals with the needed skillsets, batting to their strengths, but don’t fool yourself thinking you have Quality
group when you don’t.
When you do create a balanced Quality
team with both sides of the coin, that’s when you can really make a positive difference: a difference to your customers, business and I can tell you personally, at times yourself.
And that’s real job satisfaction, and one without a clip-board in sight.
[1] Brown, A., Eatock, J., Dixon, D., Meenan, B. J. & Anderson, J. 2008. Quality and CI in medical device manufacturing. The TQM Journal, 20, 541-555.