“ I’m sorry Prime Minister, but failure is an option. “
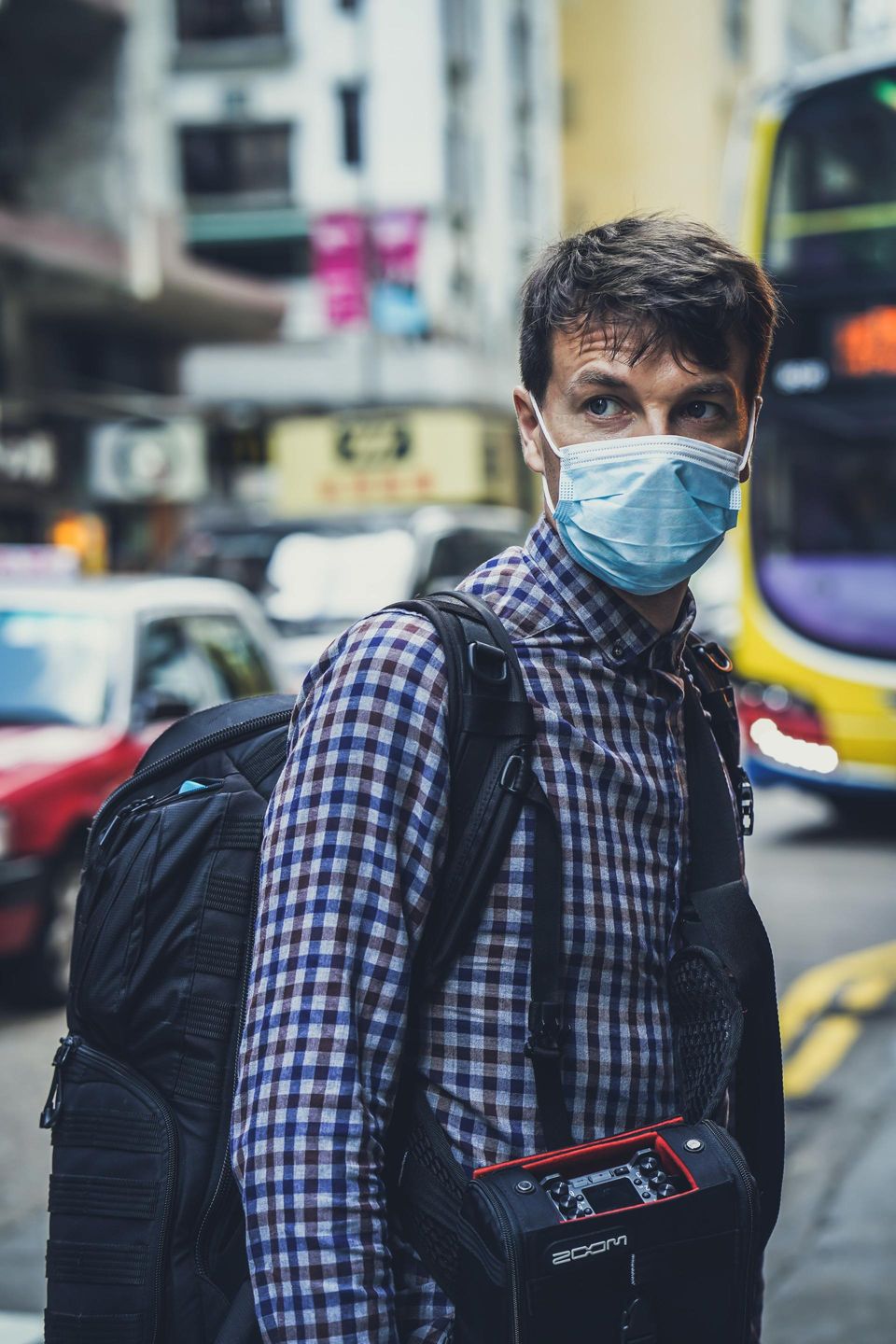
One of the concepts within the application of lean within transactional systems is the attribute of “Failure demand” . This is defined as demand within the system caused by the failure to deliver something correctly for the customer - be it processing an order incorrectly, misunderstanding what the customer really needs or misplacing their order.
Through this the system creates its own demand. Work independent of the customer need is generated, as this failure is corrected, or in many cases not corrected (1).
In many respects "Failure demand" is a manifestation of the wider range of waste within all systems, waste that saps the value-stream of its ability to satisfy customer requirements and self-inflicted work is created which has no value.
Currently in the UK there is much debate on whether the country’s “ world-beating
” Test and Trace system to identify individuals exposed to the Covid-19 virus is good enough to help stop the spread of the pandemic.
Whilst Datod
is apolitical the fact that £12billion has been spent on a testing and trace system in the UK that delivers a process where over 40% of contacts are missed – and unknowingly continue to spread the virus - speaks to a system that is certainly not working effectively (2). Though it is fair to say, it is also a system not without considerable political, operational and logistical challenges.
Given the lack of transparency around the system, it is impossible to point to the exact causes of the delink between the money spent and the poor output, but one of the reasons must surely be waste within the system. It can also be argued - as some do - that economies of scale through process centralisation are myths, when it comes to driving efficiency and responding to customer demand. A decentralised approach is more aligned with current industry thinking and probably more able to agilely meet customer needs.
Focusing on waste, from the moment an individual needs to take a Covid test, to when close contacts are finally identified there are a myriad of steps prone to waste: delays, errors, duplication, confusion and data-loss amongst others.
The concept of waste is a key focus in the application of lean within manufacturing and service systems but one often overlooked within systems such as Quality Management, with its wide range of customers, expectations and interlinked processes. It is one aspect that can have huge impact on the Quality Management System's ability to deliver value to all its customers.
Datod
has just released a module of training slides that explains how the 8 wastes covered in lean can be applied with practical examples to improve the efficiency and effectiveness of the QMS. In addition it covers 14 waste types focussing around transactional processes of the QMS, often not covered in the broader application of lean to the QMS.
The truth is that all systems never improve themselves without injection of applied energy, and without such commitment they become inefficient, ineffective and wasteful. Doing nothing is always an option, and so is encouraging failure and the demands that it brings.
(1) J Seddon (2020) Failure Demand https://vanguard-method.net/failure-demand
(2) G. Monbiot. 21st Oct 2020 The Guardian The government’s secretive Covid contracts are heaping misery on Britain.
https://www.theguardian.com/commentisfree/2020/oct/21/government-covid- contracts-britain-nhs-corporate-executives-test-and-trace